Right First Time and Cost of Poor Quality
A number of years ago whilst I held the role of a Quality Manager I was party to the following tale...
One of the metrics we used within the production area was that of 'Right 1st Time'. One that is quite comming within the manufacturing industry.
The process involved making items, spraying them in a colour glaze and firing them through a kiln. Once they had been through the kiln overnight, the items were taken reviewed by the dedicated 'Selection Team where they would identify which items were considered 'Right 1st Time' and remove any that required a re-spray.
The number of items requiring re-spray was very low. However, we noticed we were consuming more spray glaze than usual and couldn’t understand why, especially when the 'Right 1st Time' percentage was so high. This promted us to start an investigation into the root cause.
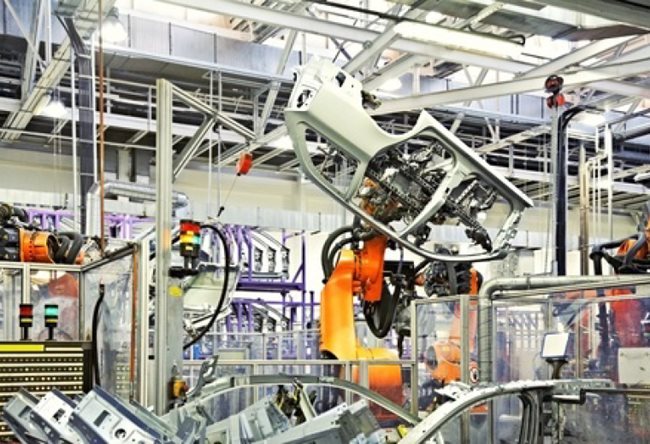
One morning I came into work earlier than usual in order to witness the kiln cart offload and I saw the Spray Glaze Departmental Manager unloading it himself. I asked him why he was doing this and he said he was pre-selecting the items which would require re-spray and taking them back into his department for re-work with the aim of speeding up the process.
When I asked him if he recorded this at all he responded with "no, there is no need as they will be in the next day's Right 1st Time figures".
It was only after a discussion with him and understanding how long he had been doing this that we realised why the consumption of glaze was so high and the percentage of 'Right 1st Time' was always so good – the Selection Team never saw the full quantity of products which had been through the kiln and the 'Right 1st Time' items may well have already been re-sprayed a number of times and travelled back through the kiln. This was all adding cost to the items before they were deemed good enough quality to be submitted to the Selecting Team.
Once we had pinpointed the issue with the re-spray, the team was then able to calculate the correct and true percentage of 'Right 1st Time' items and then further investigate the issues as to why the spray glaze process was problematic.
In order to improve efficiencies a series of measures were introduced to the organisation which included additional cleaning of the spray heads/nozzles and additional training for staff in the department.
Once we had achieved a successful new process, this along with identifying the most appropriate quantity of glaze needed plus the spray patterns, ensured that the department could fully manage the output costs and quickly identify when there was something wasn't working as expected. In turn this meant they could then resolve any issues more quickly.
The 'Right 1st Time' method and counting the real cost of poor quality is an essential measure for any production process. If low figures or high consumption of raw materials is to be avoided, all areas of the business must be involved and working as a team so as ensure the highest productivity is achieved to the highest standards possible.
The moral of this tale is that hiding the truth of poor figures might mean that the costs of the business are significantly higher than they need to be. And ultimately you might find that this may be rectified with some investigation and process modification, giving you correct results and cost efficiencies.
Author: Karen Whitby - NQA Regional Assessor
The process involved making items, spraying them in a colour glaze and firing them through a kiln. Once they had been through the kiln overnight, the items were taken reviewed by the dedicated 'Selection Team where they would identify which items were considered 'Right 1st Time' and remove any that required a re-spray.
The number of items requiring re-spray was very low. However, we noticed we were consuming more spray glaze than usual and couldn’t understand why, especially when the 'Right 1st Time' percentage was so high. This promted us to start an investigation into the root cause.
One morning I came into work earlier than usual in order to witness the kiln cart offload and I saw the Spray Glaze Departmental Manager unloading it himself. I asked him why he was doing this and he said he was pre-selecting the items which would require re-spray and taking them back into his department for re-work with the aim of speeding up the process.
When I asked him if he recorded this at all he responded with "no, there is no need as they will be in the next day's Right 1st Time figures".
It was only after a discussion with him and understanding how long he had been doing this that we realised why the consumption of glaze was so high and the percentage of 'Right 1st Time' was always so good – the Selection Team never saw the full quantity of products which had been through the kiln and the 'Right 1st Time' items may well have already been re-sprayed a number of times and travelled back through the kiln. This was all adding cost to the items before they were deemed good enough quality to be submitted to the Selecting Team.
Once we had pinpointed the issue with the re-spray, the team was then able to calculate the correct and true percentage of 'Right 1st Time' items and then further investigate the issues as to why the spray glaze process was problematic.
In order to improve efficiencies a series of measures were introduced to the organisation which included additional cleaning of the spray heads/nozzles and additional training for staff in the department.
Once we had achieved a successful new process, this along with identifying the most appropriate quantity of glaze needed plus the spray patterns, ensured that the department could fully manage the output costs and quickly identify when there was something wasn't working as expected. In turn this meant they could then resolve any issues more quickly.
The 'Right 1st Time' method and counting the real cost of poor quality is an essential measure for any production process. If low figures or high consumption of raw materials is to be avoided, all areas of the business must be involved and working as a team so as ensure the highest productivity is achieved to the highest standards possible.
The moral of this tale is that hiding the truth of poor figures might mean that the costs of the business are significantly higher than they need to be. And ultimately you might find that this may be rectified with some investigation and process modification, giving you correct results and cost efficiencies.
Author: Karen Whitby - NQA Regional Assessor