What Is ISO 9001?
ISO 9001 certification is a well-known and respected business standard. It can be a way of showing your clients your commitment to your staff, team member training, services, equipment and facilities. NQA discusses the latest ISO update in detail.
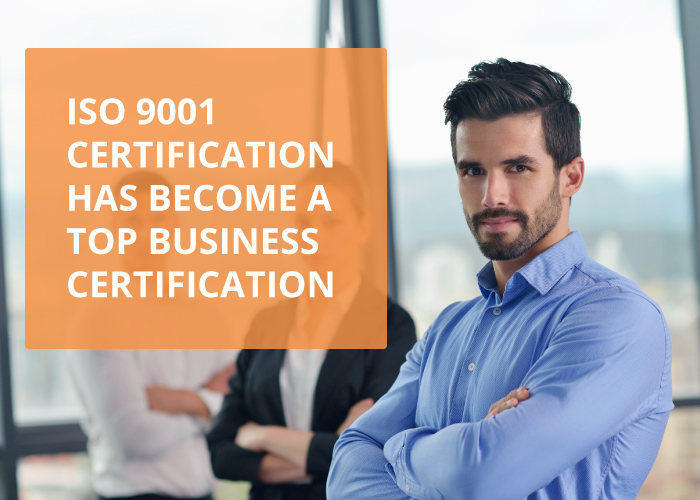
What Is ISO 9001?
ISO 9001 certification is a well-known and respected business standard. It can be a way of showing your clients your commitment to your staff, team member training, services, equipment and facilities. It encourages organizations to make constant improvements and involve all stakeholders in the process.
Obtaining and displaying the ISO 9001 certification means your company has properly implemented a protocol that meets quality management system standards. Not only will you show customers a smart face for business, but you’ll also have a complete management process and review paradigm that can help you compete in any situation.
An important note about ISO 9001 and the new 2015 standard is that certification requires the support of an entire organization. You’ll need management and leadership support for all of the required elements, not just leadership who turns over controls to quality teams.
ISO 9001 certification requires you demonstrate the ability to meet regulatory and industry requirements plus apply the quality management system standard in definable, measurable ways that help/support your customers.
It’s important to note ISO 9001 is part of the family of quality management ISO 9000 certifications and standards. As a group, this family addresses a variety of quality management systems (QMS) and best practises with tools and auditing processes.
When used in conjunction with each other, the family can guide the implementation of a quality management system standard, make it more efficient, and create a paradigm for reporting, reviewing and auditing that customers can use.
The ISO 9001 standard is the best starting point because it sets the foundation of a QMS. Let’s jump into the ISO 9001 certification process by looking at the latest update: the 2015 standard.
The New ISO 9001:2015 Standard
Released in late 2015, the ISO 9001:2015 standard is the culmination of a three-year update to the previous ISO standard. It develops and provides the criteria needed for a business-appropriate QMS, with an emphasis on performance.
In broad terms, the ISO 9001:2015 standard helps a company establish a QMS and its processes so you can implement, maintain and continually improve the QMS relative to your business. Each organization is required to determine the quality management system standards that best fit for their organization by looking at risk and opportunities as well as the best methods to address them.
As the standard has evolved, there has been less reliance on specific systems and paperwork to help companies implement best QMS practises. Instead, the ISO 9001 development has focused on managing processes and helping leadership determine what are the top methods to check any of their company’s activities.
ISO 9001:2015 took an additional step away from prescribing documentation with the introduction of a stronger Plan-Do-Check-Act (PDCA) cycle that must be applied at every level of an organization.
PDCA Cycle
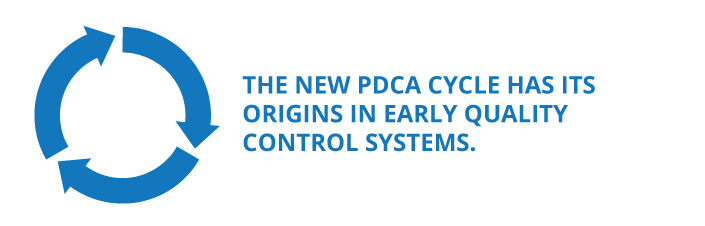
The new PDCA cycle has its origins in early quality control systems where the goal was to implement change in a way that could generate repeatable improvements. The most important aspect of the PDCA cycle for your business is that it must be developed in a way you can apply to multiple problems.
The ISO 9001 standard creates a QMS that can be used across the lifetime of your organization, so it necessitates a PDCA cycle that works as more than just a quick fix or a one-off change.
The planning stage of the cycle begins by identifying your processes, customer requirements and goals. With this information you can develop quality policies and objectives to ensure you’re delivering a good product and it is achieving your metrics.
Planning will also cover an implementation strategy to help your products meet the goals you set.
Aspects to cover in the planning stage include:
- How to generate your service or create the product
- Identification of all resources you need, including people and parts
- How each resource should be used
- What practical steps are needed to implement the plan
In the “do” piece, your business needs to execute the identified goals and steps from your planning stage. Move through these steps as you address product and service requirements that arise as you develop your offering.
This stage also covers operational basics such as designing and developing goods, making required purchases, and using parts or upgrades to achieve your desired results. When elements don’t conform to your planned goals or customer’s requirements, they should be addressed in this stage.
Through certification, you’ll also get an idea of what processes, services, software and other elements are needed not only for development but also for quality controls,
Culminate your efforts in the do phase by performing everything that is needed to make and supply the product you’re delivering to customers. From production lines for consumer goods to business execution plans for intellectual services, you’ll end with a clear picture of how to proceed for each product if this phase is done currently.
The heart of your QMS lives in the check stage. This is where you’ll need to develop quality management system standards that are a right fit for your organization. In this phase, you’ll be monitoring both your QMS and your production or service delivery.
The ISO 9001 standard and certification process will prepare you to:
- Review each element of your development to ensure it meets goals
- Make sure you’re running a process that is adequate and effective
Auditing is a significant portion of this phase, and it can include both internal audits of your processes as well as customer-based audits of your functions. You can get a clear picture of your overall system success and effectiveness by pairing audits with data analysis from reporting systems.
Checking your processes ends with a review and assessment that identifies errors or missed opportunities and makes data-based recommendations to fix these issues. Even if your products are being created properly, the check phase may help you identify areas where you can be more efficient and provide better value for your customers.
After a strong review and audit, it’s time to put identified steps into action. This phase involves a process designed to separate out issues identified in analysis and put each into a replacement, update, maintenance and improvement cycle.
ISO 9001 certification will teach you how to define corrective actions for each error plus develop a plan of preventative actions for future cycles in order to eliminate the true causes of existing or potential nonconformities.
You’ll apply every step through the QMS to verify it can achieve your desired outcome. Actions should be scheduled relevant to the immediacy of the need, but there is no room to identify problems and not take corrective action.
Plan Again!
The Act cycle identifies the solutions you’ll need to take to address problems and starts you on the path of making those corrections. However, the ISO 9001 standard is an ongoing process and must be used to evaluate the corrections you’ve made.
Run through the cycle again with each change and ensure you’ve properly addressed the culprit behind inefficiencies and other problems. Repeatedly applying your quality management system standards ensures your organization is optimising resources and promoting top quality.
You’ll be required to prove the ability to run through the entire cycle and then how your QMS dictates you move recent changes through the cycle again in order to receive ISO 9001 certification.
What’s New in the ISO 9001:2015 Standard?
The updates in the ISO 9001:2015 standard were part of a standard review and are designed to streamline the overall support provided by a QMS while improving efficiencies in the review process. "We are just bringing ISO 9001 firmly into the 21st century. The earlier versions of ISO 9001 were quite prescriptive, with many requirements for documented procedures and records," said ISO Subcommittee Chair Nigel Croft. "We have now gone a step further, and ISO 9001:2015 is even less prescriptive than its predecessor, focusing instead on performance. We have achieved this by combining the process approach with risk-based thinking, and employing the Plan-Do-Check-Act cycle at all levels in the organization."
The re-organization of the cycle to apply to all levels of a company caused a slight lengthening of the ISO 9001 standard with better definitions for its practise areas and applications.
Changes typically will help you adhere to a framework for applying the standard consistently across more business units and to meet other industry-specific standards you may face. While the change expands some activities and reorganizes their introduction, it’s unlikely you’ll face any major hiccups when moving an existing QMS over to the new layout defined by the ISO 9001:2015 standard.
The QMS Is Central
In the update, your quality management system is no longer separated into different processes. All elements of the QMS and processes it involves are unified to bring the process-based approach to a higher level of importance.
The ISO 9001:2015 documentation provides a cleaner look at how changes are to be identified within a QMS framework and how processes play a role in further development. You’ll still see standard requirements such as defining customers and objectives for each department, but flexibility in authority for addressing complaints is a notable change.
The overall goal for this change was to make it easier for you to identify elements in need of change because of efficiency concerns as well as customer satisfaction.
Risk Assessment Updates
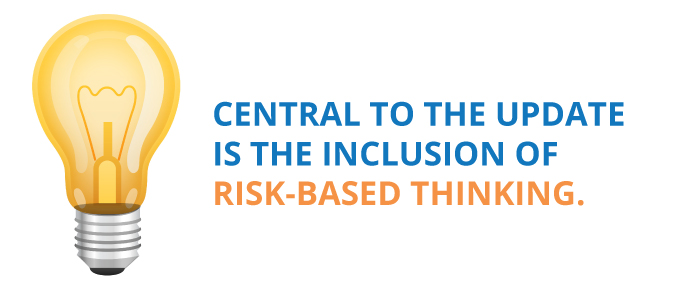
Central to the update is the inclusion of risk-based thinking.
This type of thinking will allow you to “determine the factors that could cause its processes and its quality management system to deviate from the planned results,” the guide notes. It also gives you help to put preventative controls into place to mitigate risks and maximize opportunities across dynamic environments.
This boils down to a stronger emphasis on performance monitoring from all levels of management.
One area that may be somewhat of a surprise to new practitioners is the inclusion of positive risks:
- These are elements that are defined under risk-based thinking models that provide opportunities to improve your organization.
- Risks are both large and small and may provide a significant competitive advantage if they can be achieved.
A good element of the ISO 9001:2015 standard framework is that you will learn how to assign values to positive and negative risks, ensuring you tackle the biggest problems first or start improvements with changes that run the smallest chance of doing harm to your business.
Downsizing Documents
The International Organization for Standardization also changed the ISO 9001 to adjust to modern business needs. New software, data gathering tools and modern analytics that rely on modelling and machine learning make it nearly impossible to apply a uniform standard for reporting.
To meet that change, the ISO greatly reduced its rigid documentation requirements. Your company can now use the documentation format you prefer, and you can determine the best data to include to give you proper guidance for changes and improvements.
The ISO 9001:2015 standard changed so significantly that it even no longer requires a prescribed quality manual.
However, that doesn’t mean reporting has taken a backseat. The standard outlines processes to use in recording and how reports must be utilized throughout your QMS.
Companies that have currently been verified under the ISO 9001:2008 standard will have three years to meet the new 2015 requirements.
What Are the Benefits of Being ISO 9001 Certified?
ISO 9001 certification is a competitive advantage because it shows existing and potential clients that your organization values management, operational efficiency and customer support.
Because the process requires you to demonstrate real-world situations where your quality management system provides customer benefits, you can also use the certification process as a case study for how you go above and beyond to address customer concerns.
Benefits your customers see can include:
- More on-time deliveries.
- Customer service support designed around common questions.
- Reduction in product and service complaints or returns.
- Simple audit process with easy reporting.
- Qualified support as their business grows and moves into new markets.
Benefits your brand may see when attaining ISO 9001 certification:
- Clean, effective management process for senior leadership to follow.
- Tools to identify and enact time-saving processes.
- Marketing opportunities to tell customers of your commitment in a language they understand.
- Audit processes that can call out areas of financial savings and waste.
- Well-defined responsibilities of each business unit and their reporting requirements.
- Meeting requirements for attaining federal, state and local municipality contracts.
- Help creating a cycle of assessment, upgrades and business supports.
- Report integration with some new software for data-driven insights.
Perhaps the strongest benefit of ISO 9001 certification is it can provide you with insight and savings regardless of your size. The ISO 9001:2015 standard is able to perform well across any organization because it naturally segments into business units and processes.
Essentially, large organizations are split into smaller, controllable units by the QMS processes. Smaller organizations can be treated as one of these units, allowing QMS best practises to be applied and full benefits to be actualized.
3 Steps to Certification
ISO 9001 certification remains a very straightforward process, even with the 2015 standard update. An authorized certification body will still review your internal processes and ensure your quality management system meets prescribed standards.
The full review is a three-step process:
- It starts with an application request. You’ll need to complete an ISO 9001 quotation request form so they can start the review process. The forms detail your organizational structure, what activities you want covered by certification, current certification status and the complexity of your organization processes.
- After that, the certification body will perform an assessment that includes two mandatory visits for an initial certification audit. During these assessments, you’ll need to show your QMS has been fully operative for at least three months and you’ve performed a full cycle of internal audits. Specific testing and samples may be requested.
- If you pass the audits, you’ll receive your certification from NQA – a UKAS/ANAB accredited certification body. We recommend that you then adopt a maintenance programme of annual surveillance audits to ensure you stay on top of advancements and don’t let your QMS fall into disuse. You can also schedule the re-certification audit required every three years.
Planning ahead allows you to meet each requirement. Proper implementation governed by the ISO 9001:2015 standard gives you the perfect prescription for implementing a QMS that becomes a part of your company’s culture.
Risk management is the new requirement for every partner, whether they supply a single add-on product or are at the core of a supply chain. Companies are running leaner and demanding more of their partners each day, making the adoption of the ISO 9001 certification as much of a must-have as it is a true competitive differentiator.
Start Your Certification Process Today
NQA provides an easy ISO 9001 certification process that will ensure you meet all of the standard’s objectives or provide you with a clear action plan to become a certifiable organization.
To help you get certification-ready, we offer Gap Analysis that can look at your organization for areas of improvements or areas where you may not have made the right changes to adhere to the new ISO 9001:2015 standard.
Our experts can also help you decide what the best ISO 9001 certification is for your brand. We currently execute both 2008 and 2015 standards certification. While a full conversation is recommended to help you choose, there are some benefits that each provide.
Begin the ISO 9001 Certification Process
Start your ISO 9001 certification process today by working with NQA. Get your free quick quote today to learn how much you can save as you implement a process that quickly will turn into a competitive advantage.
Reviewed by: Terry Fisher, NQA Occupational Health & Safety Principal Assessor