Complete Guide to Quality 4.0
Technology has long been a driver of industrial changes, from the Industrial Revolution's introduction of large-scale production to today's use of automated work environments and artificial intelligence (AI). Quality control measures have likewise needed to adapt to the growth of technology to ensure production and products meet specific requirements.
The Evolution of Quality
The first two stages of industry, Industry 1.0 and 2.0, focused on maximizing production as people adapted to using machinery in factories to increase output. With Industry 3.0, which started in the 1940s, the quality of goods became more important as brands sought to differentiate themselves from the competition. This stage lasted through 1995 and focused on optimizing customer satisfaction.
By the mid-1990s, technology allowed for the introduction of Industry 4.0. This manufacturing revolution used machines that could self-learn, communicate with other devices to coordinate production and shift human operations to roles that require human discernment, such as designing systems.
The communication capability of machines tightens the system to close areas where humans have an influence on the production process. Therefore, the design of the process becomes critical to identifying areas that could cause potential quality issues. Without this overview, products could pass through most of the supply chain automatically before problems with the process or products become clear. Quality 4.0 looks at the process from the design phase forward to prevent problems before they happen.
With automation taking over industrial operations in Industry 4.0 and changing worker roles, similar changes happened to quality management. Quality 4.0 leverages the most up-to-date technology in improving operations and products. This application can include automating quality processes with self-learning machinery to reduce mistakes and supply chain problems.
As the manufacturing industry has evolved to embrace automation and connectivity of systems by shifting to Industry 4.0, quality professionals have needed to make changes in how they work. Quality 4.0 makes the most of the technology available to hone processes from the design level to reduce risk and improve production.
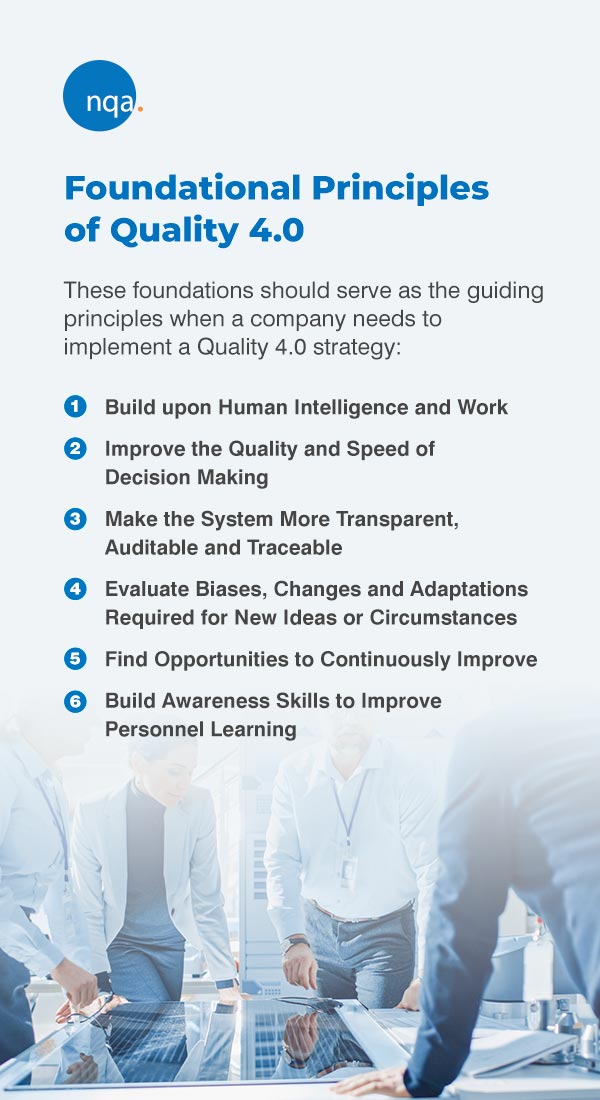
Foundational Principles of Quality 4.0
Quality 4.0 does not have a standardized definition. However, it does have various traits and values that appear in many descriptions of the system. The drivers behind Quality 4.0 involve using technology to help people improve their job processes more than ever.
These foundations should serve as the guiding principles when a company needs to implement a Quality 4.0 strategy:
1. Build upon Human Intelligence and Work
Technology will not eliminate the roles of humans in the organization, but human work and intelligence will take new positions in operations. Human jobs within Quality 4.0 become even more critical because they require careful judgment of situations. Using the best of human intelligence to identify areas of planning, change and adaptation allow companies to produce process designs that minimize mistakes.
2. Improve the Quality and Speed of Decision Making
Decision-making must keep up with the lightning-fast automated speed of processes. Making the right choice in as little time as possible, both for humans and machines, requires having ample, reliable data. Quality 4.0 relies heavily on data collection for supporting decisions throughout the operation.
3. Make the System More Transparent, Auditable and Traceable
Systems under Quality 4.0 become more traceable and transparent, making them readily auditable in cases of recalls or other concerns. By tracing production, the exact point of an error can appear quickly, making fixing issues less time-consuming.
4. Evaluate Biases, Changes and Adaptations Required for New Ideas or Circumstances
Quality 4.0 is the current and future of quality management. Therefore, those who use this system will need to address new ideas and circumstances as the definition of Quality 4.0 solidifies with time and technology. Organizations must find areas where they have existing biases to address those leanings and make the necessary alterations to their operations to adapt.
5. Find Opportunities to Continuously Improve
Improvement is not a one-time task. Quality continues to get better with time. With the data collected via the technology used in Quality 4.0, quality managers can more easily find areas and opportunities to improve.
6. Build Awareness Skills to Improve Personnel Learning
Everyone needs to become self-aware to better understand how they can educate themselves on the new ideas and innovations introduced over time. This awareness becomes an on-the-job skill that will improve adaptability to acquiring new knowledge.
Artificial Intelligence and Process Automation
The automation of quality processes relies on tapping into big data. Using sensors to collect large amounts of data across a manufacturing floor was impossible before the use of effective AI. AI can gather, analyze and use data to predict outcomes and boost quality and productivity.
Artificial intelligence's ability to generate predictive analytics improves the work of human decision makers. AI can sort through large amounts of data from individual records, including unstructured information. The system can analyze and categorize the information to show probabilities of critical elements, such as complaints or quality events. Quality management uses this consistent categorization of data to make better decisions.
Similarly, AI can examine quality events and responses across the entire set of collected information to categorize and suggest potential actions based on prior outcomes. Again, this system augments the efforts of human decision makers to take the statically best action in response to quality events, such as audits, complaints or non-compliance.
Checking quality only after automated production can lead to large batches of problematic products that may require future recalls. AI can examine the operations of automated manufacturing systems in real time and alert quality management of production abnormalities, allowing production to stop quickly to correct the issue before costly mistakes occur.
AI does not replace people within quality management — it helps them to do their work better. People rely on AI capability to use big data to create the necessary environment required to automate processes that maintain quality.
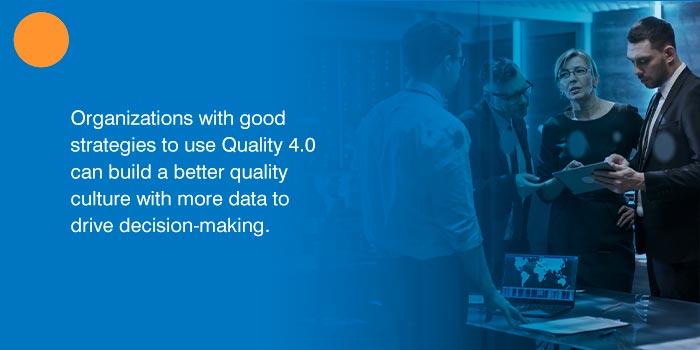
Creating a Quality 4.0 Strategy
Creating and implementing a Quality 4.0 strategy requires focusing on people, processes and technology. Organizations with good strategies to use Quality 4.0 can build a better quality culture with more data to drive decision-making.
Using technology to collect large amounts of data improves the quality of the information used. Therefore, the Quality 4.0 framework of any organization must include building on the technology used to ensure it can support the data collection, analysis and predictive requirements of the future of quality culture.
1. Identify Processes and Other Areas that Could Benefit Most from Quality 4.0
To effectively make the most of Quality 4.0, it needs to have targeted use within your processes and quality goals. Setting goals for the organization's quality will facilitate the applications it needs to fulfill those objectives. For example, an organization may need to use AI to analyze its structured and unstructured data to improve decision-making based on the AI's predictive analysis of the information.
Another potential application of Quality 4.0 is connecting enterprise and operational systems to improve data gathering and sharing. Specifying the areas for use allows for the creation of a plan that reduces wasted expenses while getting more out of the upgraded technology and its applications.
2. Focus on the Most Useful Aspects of Quality 4.0
Quality 4.0 has multiple applications, not all of which will work well in every organization. Focusing on integrating the most useful of its core components will reduce costs in implementing Quality 4.0 and improve acceptance of the upgrades.
Common components of Quality 4.0 an organization can choose from include the following:
- Harnessing data to drive evidence-based decision-making
- Using analytics to make sense of big data and improve decision-making
- Connecting operational and enterprise systems for improved communication about operations
- Collaborating throughout the supply chain through blockchain technology and other traceability technologies
- Using digital quality management systems to maintain and track data across product life cycles and develop quality processes
- Streamlining and automating compliance work through applications of technology
- Scaling quality development efforts through company growth with Quality 4.0 tools such as data lakes or cloud computing
- Improving employee training and knowledge bases through better competency activities that impact quality
- Developing apps using virtual reality (VR) or augmented reality (AR) to boost quality activities within the organization
- Adopting tools to give all employees a part in a quality culture
Building a Quality 4.0 strategy based on choosing to focus on some of the above components will form a customized framework to best suit the organization's needs.
3. Align Quality 4.0 and Technology Adoption Goals
Quality 4.0 relies on technology for data collection, analysis and communications. In a comparable manner that the components of the system must match the needs of the organization, the technology should, too. The organization's digital maturation should correspond to the technologies required for it to expand. Organizations with already robust digital investments have better capabilities to integrate more technology-intensive Quality 4.0 strategies, such as VR or AI.
In businesses that present resistance to adopting the technology required for executing basic Quality 4.0 strategy, the quality team should find ways to convince management of the benefits for both productivity and quality in upgrading.
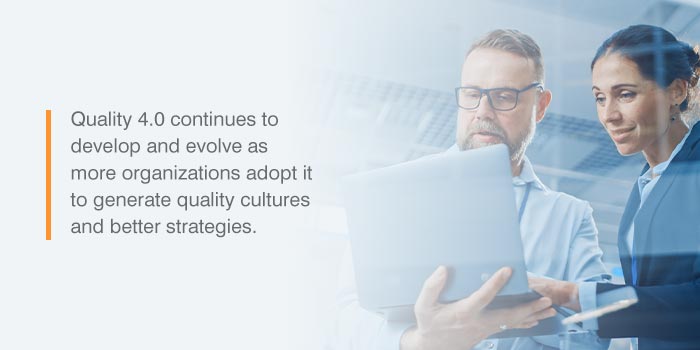
Quality 4.0 FAQs
Quality 4.0 continues to develop and evolve as more organizations adopt it to generate quality cultures and better strategies. The changing nature of this system means there are many questions surrounding general and specific concerns about using Quality 4.0:
1. What is Quality 4.0?
Industry 4.0 uses automation, artificial intelligence and machine learning to improve manufacturing processes. Quality 4.0 boosts quality by applying the same technology to quality management.
Quality 4.0 does not neglect the role that people have in process quality. It augments the work of decision makers by providing them with the information they need to make choices based on previous best outcomes.
2. Why is Quality 4.0 Important?
Quality 4.0 is not a set framework that all companies must adopt. Its fluid definition allows quality management teams to mold the use of the emerging technology to their organization's needs. In doing so, they become active members in the evolution of the organization's quality culture that integrates the best of technology for improved compliance, decision making and quality processes.
3. What is the Connection between Quality 4.0 and ISO 9001?
Quality 4.0 is a system used to improve quality, but it will not replace the ISO 9001 standard. Compliance with this standard will continue to show customers the organization puts quality into its processes and people to produce effective services or products. The core principles of ISO 9001 continue to be equally important for showing quality under Quality 4.0 as they have been in the past.
The ISO 9001 standard framework will continue to remain a staple for quality adherence, regardless of the technology used to reach those goals. Quality 4.0, however, can automate some of the processes required to attain compliance with the standard and find areas for potential improvement. By using a Quality 4.0 strategy, an organization can more easily meet the ISO 9001 standard with its culture of quality and improved operations.
4. Is Quality 4.0 the same as Quality 3.0 with a Different Name?
Quality 4.0 is different from the previous iterations of the system. Under Quality 3.0, the focus remained on improving the process operators to ensure the quality of finished products. With Industry 4.0, manufacturing becomes largely automated for the entire process, making checks along the way more difficult.
Therefore, Quality 4.0 ensures designers of the process focus on getting the quality required. Additionally, machine learning and data collection gather information about the machinery used within the process and automatically identify ways to optimize operation or alert management of issues.
5. Will Quality 4.0 Threaten Quality Management Jobs?
Quality 4.0 does not threaten jobs within quality management. Instead, it changes the definitions of what professionals in those roles do. Professionals under the new system will become advocates for adopting the technology and tools needed to create a quality culture. They will also use the data and analysis collected to make better decisions in improving process quality.
Quality management jobs continue to be vital components of organizations. They serve as the drivers behind the Quality 4.0 strategy the organization uses and how the company implements its use. The technology used by Quality 4.0 only supports human roles and helps improve decision-making instead of replacing the need for human discernment.
6. Is Quality 4.0 the Future of Quality?
The future of quality may not stop at Quality 4.0. Improving industrial processes and quality go hand-in-hand, and as manufacturing changes, so will quality controls. For now, organizations looking to boost quality, transparency and traceability within the more efficient and productive Industry 4.0 should adopt elements of Quality 4.0 into their quality management systems.
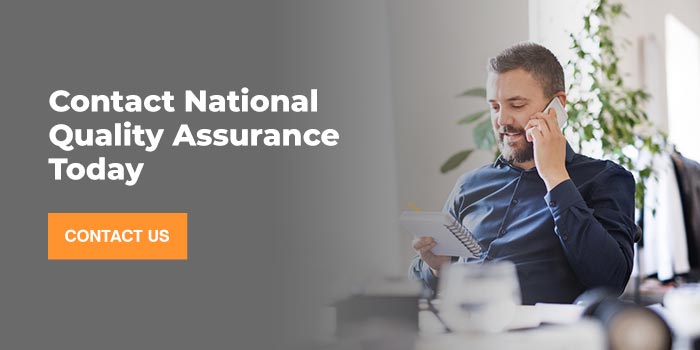
Contact National Quality Assurance Today
Find out more about how NQA can help you improve your products and services to receive accreditation. Fill out our contact form to get in touch with one of our team members.