Health & Safety Management Training (ISO 45001)
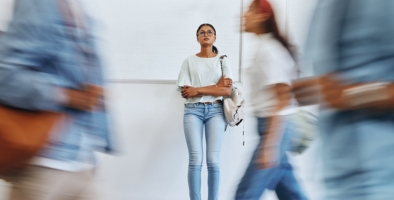
NQA ISO 45003 Introduction Training
E-Learning (Psychological H&S)
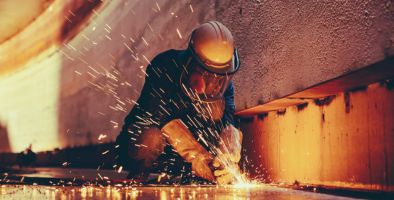
NQA ISO 45001 Introduction Training
E‑Learning (Health & Safety)
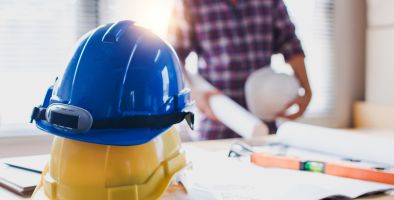
NQA ISO 45001 Introduction and Implementation Training
Virtual - Tutor Led (Health & Safety)
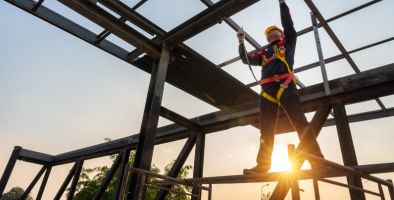
CQI and IRCA ISO 45001 Internal Auditor Training (A2199)
Virtual - Tutor Led (Health & Safety)
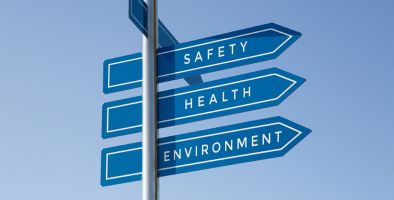
CQI and IRCA ISO 45001 Lead Auditor Conversion Training (A1918)
Virtual - Tutor Led (Health & Safety)
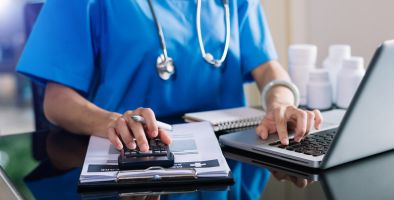
CQI and IRCA ISO 45001 Lead Auditor Training (A2236)
Virtual - Tutor Led (Health & Safety)
Occupational Health & Safety Management Training (ISO 45001)
ISO 45001 is the first global Occupational Health and Safety (OH&S) management system standard to adhere to the ISO Annex SL structure and replaces the widely implemented OHSAS 18001 (which was withdrawn in September 2021).
Our range of ISO 45001:2018 training courses have been developed with the aim of helping you to improve workplace safety and. They will give you the tools and knowledge to identify, understand and manage your OH&S risks and to improve overall business performance and processes.
Our ISO 45001 Health & Safety courses are designed to help you:
-
Develop and implement an H&S policy and objectives
-
Establish processes which consider ‘context’
-
Identify and manage risks, opportunities, legal and ‘other’ requirements
-
Determine the hazards and OH&S risks associated with your activities
-
To put in operational controls to reduce injury and ill-health
-
Improve your business performance and reputation
Booking your place on one of our ISO 45001:2015 Health & Safety Management Training courses is the first step towards achieving and maintaining UKAS accredited certification for your organisation’s OHS Management System.
Our range of ISO 45001 (OHS) training delivered by expert tutors will help you to understand what a Health and Safety Management System is, how to implement and maintain it, and how to effectively audit your system through practical knowledge sharing and industry leading tools.
NQA is also a proud CQI and IRCA Approved Training Partner, and you can find many CQI and IRCA certified courses within our portfolio.
Why Choose ISO 45001 Training?
Did you know that UK businesses lose over 31 million days every year due to work-related illnesses and injuries?
Our interactive ISO training provides delegates with the know-how to reap the benefits of implementing an efficient Occupational Health & Safety (OH&S) management system to reduce those work-related absences and incidents.
The courses aim to support your organisation’s understanding of the internationally recognised standard by improving your reputation as a safe place to work.
You’ll learn about how to introduce and implement an ISO 45001 management system and then follow on with how to conduct internal audits to help you identify and reduce risks. For the more advanced professional our courses can also help you become a certified Lead Auditor.
Different Ways to Learn
NQA offer e-Learning, virtual, public and in-house ISO 45001 training options to suit all learning styles and needs. Whether you are looking for an Introduction to the standard, want to know how to audit your own system or are looking for a more advanced Lead Auditor course.
Although much of our training is currently being held virtually, we are in the process of re-introducing some options for face-to-face public courses for those that like to interact in person with others. Keep an eye out for those coming soon.
ISO 45001 e-Learning
Our ISO 45001 e-Learning course provides the essential basis for understanding the key elements of ISO 45001:2018, the international standard for Environmental Management Systems. From this foundation you can build the skills to implement, audit and optimise an effective environmental management system and consists of on-demand learning, downloadable takeaways and a short test. It can be completed in as little as a few hours.
ISO 45001 Virtual Training
We are continuing to run all our courses virtually so that you can attend from the comfort of your own home or office, anywhere in the country.
The training sessions are designed to give you the knowledge you need to advance and grow and are delivered by industry experts. You’ll have the chance to interact fully with both the host and other delegates over Zoom for a rounded and immersive experience, just like you would in a classroom.
ISO 45001 In-House Training
If you have a slightly larger group we can offer training at your premises, which may prove more cost effective for you. This means that we can also ensure the training is tailor-made to your needs and requirements.
Benefits of In-House ISO training:
-
Cost effective and efficient – team learning reduces cost-per-head and increases return on investment from your training budget.
-
Total flexibility – we deliver in-house training where and when you want in the format you need; from briefing sessions and workshops to examined courses to meet your specific objectives.
-
Relevant and practical – our tutors are management systems practitioners with extensive experience of implementation, auditing and continual improvement. They’ll ensure that concepts and techniques are clearly understood and adopted.
-
Team building – training in teams achieves common learning objectives, improves collaboration and increases the adoption of new techniques in practice.
-
Personalised services – we take the time to fully understand your training needs and match our expert tutors to fit your organisation.
Request an In-House training quote here
Consultancy Services
After sitting on your ISO 45001 course, if you find that you might like further help with achieving certification or maintaining your management system then talk to us about our Associate Partner programme (APP). We can give you access to our fantastic database of knowledgeable consultants.Further Guidance and Handy Resources
-
For more information on the ISO 45001:2015 OHS Standard why not take a look at our FAQ section.
-
For more information on the courses we offer, call 0800 052 2424 (option 3) and speak to a member of our team or email us at training@nqa.com.
-
To learn more about certification, please sign up to our free webinars.
-
Are you wondering which type of NQA training course is most suitable for you? Our Journey Guide will point you in the right direction.
ISO 45001 Training Reviews
"I have attended a couple of ISO Lead Auditor courses over the last few months and I found this one to be the best, the tutor was excellent." HMS Auditing Services Ltd - CQI and IRCA ISO 45001 Lead Auditor Conversion Training
"The tutor presented this course very clearly and concisely which gave me the confidence to go and conduct value added audits in my own workplace." Monks & Crane Industrial Group Holdings - CQI & IRCA 45001 Internal Auditor Training